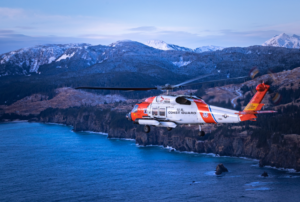
An MH-60T Jayhawk conducts operations around U.S. Coast Guard Air Station Kodiak, Alaska. Photo from DVIDS.
When the U.S. Coast Guard was unable to procure a wiring system part that affected its entire fleet of MH-60T helicopters in late November, they turned to the Naval Air Systems Command (NAVAIR) Additive Manufacturing (AM) Team.
Thanks to a collaborative workplace culture between services and a recognition for urgent solutions at the time of need, the Coast Guard kept its aircraft flying without a break in operations.
As members of the Coast Guard prepared to upgrade the MH-60T Automatic Asset Tracking System’s (AATS) wiring system and distribute it to the fleet, they noticed one item was missing. “All the parts must be in the kit before the upgrade is pushed out to the fleet,” explained Lt. Cmdr. Andrew Armstrong, Surface Forces Logistics Center Industrial Operations Division National Industrial Enterprise, Organic Depot Maintenance branch chief and Surface Fleet Additive Manufacturing lead. “One unique wiring part, the AATS spacer mount, was unavailable via commercial means; the only approved fabrication method to meet this need is additive manufacturing (AM),” he said.
The Coast Guard’s AM team ran into another problem after its AM shop designed, printed a prototype and began to manufacture the spacing mount. The material to 3D print it, called Black Ultem — a polyetherimide material with high mechanical strength and rigidity — was not in stock. Familiar with NAVAIR’s AM capabilities, Armstrong contacted NAVAIR AM Program Manager Ted Gronda. The Coast Guard already had an approved AM technical data package (TDP) for the part, which specified the same AM machines as NAVAIR’s. All Armstrong needed to do was transfer his TDP files via the Joint Technical Data Integration (JTDI) website, Gronda said.
The U.S. Navy, and NAVAIR in particular, has a long history of supporting other federal agencies with AM. “It’s an opportunity to strengthen relationships across organizations and create channels for future collaboration and exchange of information. We were more than willing to help,” he said.
Gronda quickly set the NAVAIR AM Team to work. Engineers determined NAVAIR’s AM systems could meet the requirements, so they authorized a deviation for printing on the AM system at Fleet Readiness Center Mid-Atlantic Detachment Oceana in Virginia Beach, Virginia, the closest NAVAIR AM system to the point of need.
However, Lakehurst did not have the thermoplastic AM material on hand. After several calls to different NAVAIR sites, the team learned the Polymers Research Branch at Patuxent River had the required thermoplastic. Of course, how to get the material to the AM machines at Oceana posed another challenge.
“Recognizing the urgency and the importance — this impacted the Coast Guard’s entire MH-60T fleet — one of our team members volunteered to drive the materials from Pax River to Virginia Beach that evening, an almost four-hour drive,” Gronda said. While the materials were being delivered, Armstrong uploaded the TDP to JTDI. Then, Naval Air Warfare Center Aircraft Division Lakehurst Additive Manufacturing Team Lead Anna Carlson modified the build file to print on Oceana’s AM system while still meeting Coast Guard drawing requirements.
Once the materials arrived in Oceana, Aviation Electronics Technician Petty Officer 2nd class Charles Oneal downloaded the TDP and began manufacturing the required parts. Within 24 hours, Oneal printed and delivered 15 AATS spacer mounts to Coast Guard representatives.
Because of the team’s collaboration, forward thinking and can-do attitude, the parts kits will go out much earlier to facilitate the required capability upgrade for the Coast Guard’s MH-60T fleet. Every Coast Guard MH-60T will carry the additively manufactured spacer as a part of the outfitting, Armstrong explained.
“This effort marked yet another extraordinarily successful example of a cross-organizational collaborative effort,” said NAVAIR AM Polymer Lead Dr. Kate Thorn. Knowing cases like this will continue to present themselves, she further noted, “We’re now documenting the process, so future needs can be expedited and standardized.”
“I appreciate the priority the Navy gave this effort,” Armstrong said. “Working together, across services, we improved the readiness of a critical asset and reduced the time required to do so.”
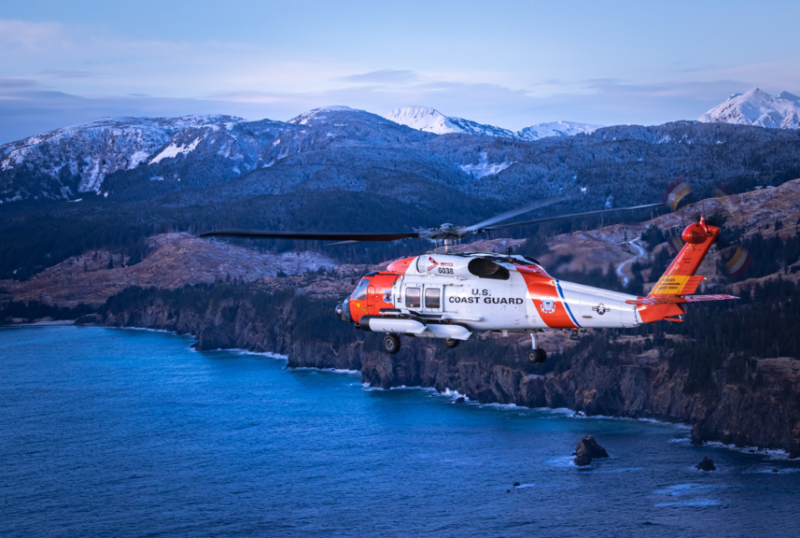
An MH-60T Jayhawk conducts operations around U.S. Coast Guard Air Station Kodiak, Alaska. Photo from DVIDS.